CNC Machined Parts Manufacturer: Revolutionizing the Metal Fabrication Industry
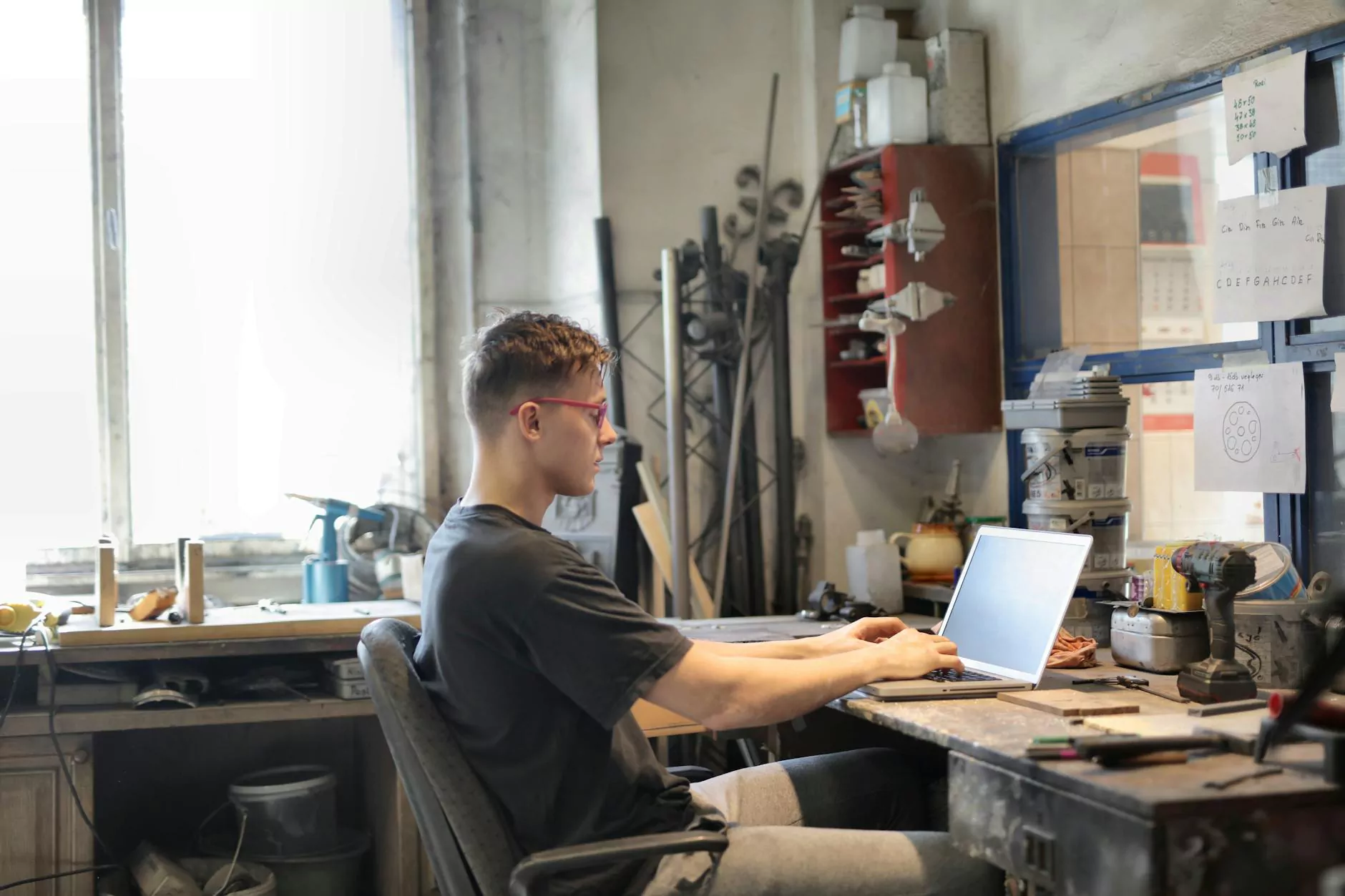
The world of manufacturing has consistently evolved, driven by the demand for precision, efficiency, and excellence in production. Among the various technologies that have emerged, cnc machined parts manufacturers stand out as pivotal players in the field of metal fabrication. This article explores the importance of CNC machining, its advantages, and how it shapes the future of manufacturing.
Understanding CNC Machining
CNC machining (Computer Numerical Control machining) is a process used in the manufacturing industry that employs computers to control machine tools. The CNC process has transformed the production of various components, particularly in industries requiring exceptional precision, such as aerospace, automotive, and medical devices.
How CNC Machining Works
The CNC machining process begins with a detailed design, typically created using CAD (Computer-Aided Design) software. After the design phase, the following steps ensue:
- Programming: The CAD design is converted into numeric code (G-code) that dictates the machine's movements.
- Machine Setup: Operators set up the CNC machine, installing the necessary tools and loading the raw materials.
- Machining Process: The CNC machine follows the G-code instructions with high precision, removing material from the workpiece to create the desired shape.
- Quality Control: The finished part undergoes rigorous inspection to ensure it meets the specified tolerances.
Advantages of Using CNC Machined Parts Manufacturers
As industries seek to enhance productivity and quality, cnc machined parts manufacturers provide significant benefits that contribute to their growing popularity:
1. Precision and Accuracy
One of the most significant advantages of CNC machining is its ability to create highly precise components. The automated nature of CNC machines eliminates human error, ensuring that each part is manufactured to exact specifications. This precision is particularly critical in sectors where tolerances are tight and failure is not an option, such as in the aerospace industry.
2. Enhanced Production Speed
CNC machines can operate continuously without fatigue, greatly improving production rates. This efficiency allows manufacturers to produce large quantities of parts within a shorter time frame, making CNC machining a preferred method for high-volume production runs.
3. Versatility in Materials
CNC machining is compatible with a vast array of materials, including metals, plastics, and composites. Manufacturers can easily adapt their processes to work with different materials, catering to diverse industry needs.
4. Flexibility in Design Changes
With minimal downtime, CNC machines can be reprogrammed to accommodate design changes or new products. This flexibility helps manufacturers stay competitive and responsive to market demands.
5. Cost-Efficiency in Long-Term Production
While the initial setup for CNC machines can be high, the long-term savings in labor costs, material waste reduction, and enhanced production capabilities often outweigh these costs. Manufacturers can achieve economies of scale, making CNC machining an economically viable option for large-scale production.
The Role of Metal Fabricators in CNC Machining
Metal fabricators play a crucial role in the CNC machining process. They oversee the transformation of raw metal into finished components, ensuring quality at every stage. Here are the pivotal tasks handled by metal fabricators:
1. Material Selection
Choosing the right material is fundamental. Metal fabricators evaluate the requirements of the final product and select materials that offer the best performance, durability, and cost-effectiveness.
2. Part Design and Prototyping
Working closely with designers and engineers, metal fabricators help design parts that can be efficiently and effectively produced using CNC machines. They often create prototypes to test designs before full-scale production.
3. Quality Assurance
Metal fabricators implement stringent quality control measures throughout the manufacturing process. They conduct inspections at various stages to ensure that every part meets the required specifications.
4. Post-Processing and Finishing
After machining, parts may require additional processes such as polishing, coating, or assembly. Metal fabricators provide these finishing touches, enhancing the final product's performance and aesthetics.
Emerging Trends in CNC Machining and Metal Fabrication
The CNC machining landscape is continuously evolving. Several trends are shaping the future of this industry:
1. Automation and Smart Manufacturing
With the rise of Industry 4.0, automation in CNC machining is becoming mainstream. Smart machines equipped with IoT capabilities can provide real-time data analytics, predictive maintenance, and enhanced operational efficiencies.
2. Advanced Materials
As technology progresses, manufacturers explore new lightweight and high-strength materials. Innovations in material science are pushing the limits of what can be produced using CNC machining.
3. Sustainable Manufacturing Practices
Environmental sustainability is a growing concern across industries. CNC machined parts manufacturers are adopting greener practices, such as minimizing waste and using recyclable materials.
4. Increased Customization
Customers today demand personalized products. CNC machining's flexibility allows manufacturers to offer customization options, catering to specific client needs without significant additional costs.
Choosing the Right CNC Machined Parts Manufacturer
When looking for a reliable cnc machined parts manufacturer, it's crucial to consider various factors to ensure you achieve the desired outcomes:
1. Experience and Expertise
Evaluate the manufacturer’s experience in the CNC machining field. Companies with a proven track record in your specific industry will better understand the demands and standards required.
2. Technology and Equipment
Ensure the manufacturer is equipped with state-of-the-art CNC machines and technology. Advanced machinery translates to better precision and efficiency in production.
3. Quality Control Processes
Inquire about their quality assurance protocols. A reliable manufacturer will have stringent quality control measures in place to guarantee the integrity of each part produced.
4. Customer Support
The level of customer service provided is essential. A manufacturer should be responsive and willing to assist you throughout the entire process, from design to delivery.
5. Competitive Pricing
While cost should not be the sole factor, obtaining quotes from multiple manufacturers will help you gauge the market rates and ensure you receive fair pricing for your requirements.
Conclusion: The Future of Manufacturing with CNC Machined Parts
In summary, the role of cnc machined parts manufacturers is increasingly vital as industries strive for efficiency, precision, and quality. The integration of advanced technology and innovative practices shapes the future of metal fabrication, making CNC machining a cornerstone of modern manufacturing. By understanding the benefits, selecting the right manufacturer, and adapting to emerging trends, businesses can thrive in this competitive landscape, driving forward innovation and excellence.
For those looking to partner with a leading cnc machined parts manufacturer, deepmould.net offers cutting-edge solutions, exceptional quality, and unparalleled customer service in the realm of metal fabrication. Explore your possibilities today!