Mastering Plastic Molding Tools: An In-Depth Guide to Success in Business
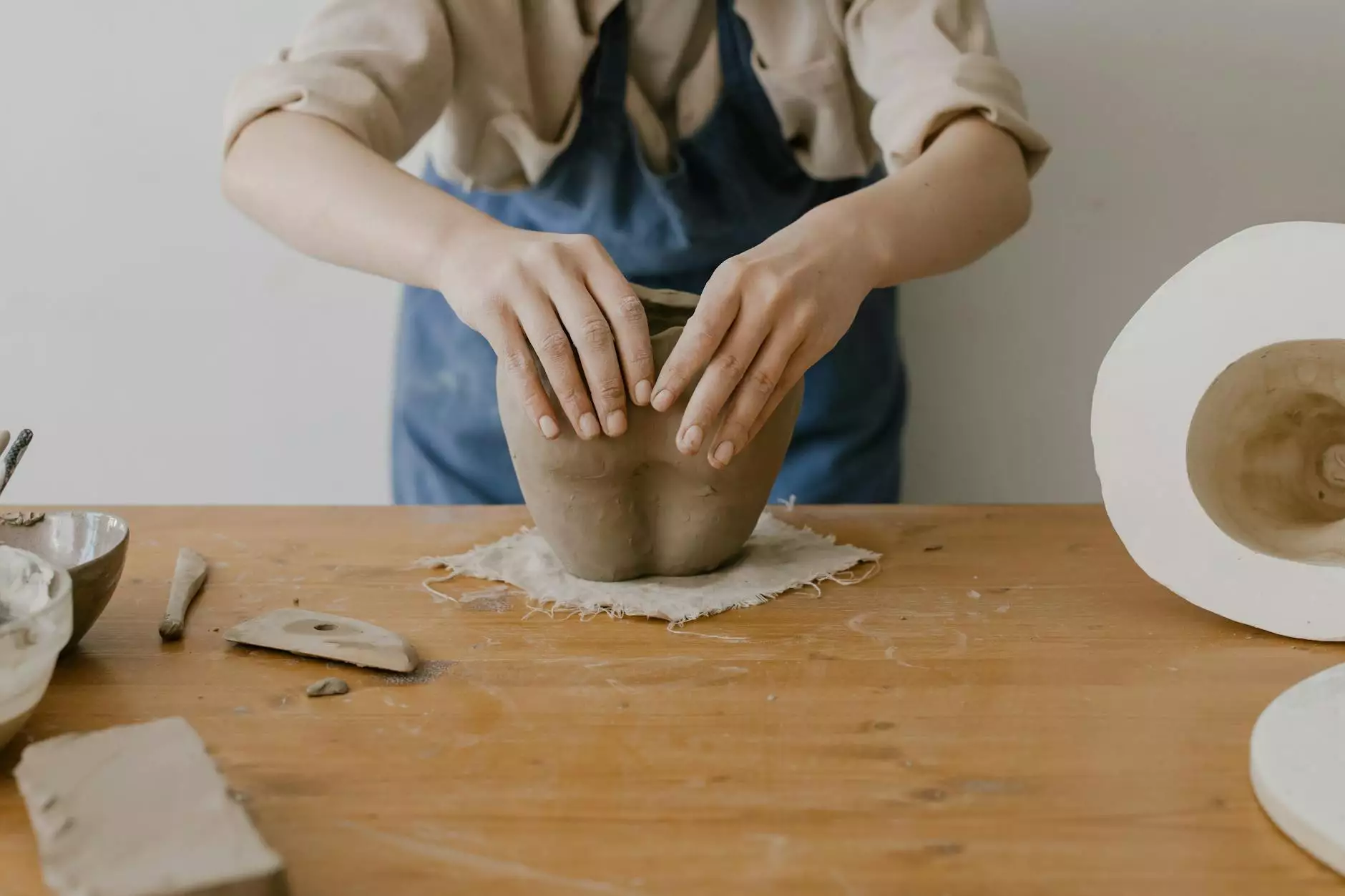
Plastic molding tools are essential assets in the manufacturing industry, especially for businesses involved in metal fabrication and plastic production. Understanding the intricacies of these tools can greatly enhance efficiency, quality, and profitability. In this comprehensive guide, we will explore the various aspects of plastic molding tools, their applications, advantages, and how they fit into the broader landscape of modern business practices.
The Significance of Plastic Molding Tools in Manufacturing
In the realm of manufacturing, the use of plastic molding tools plays a vital role in the production of a wide array of products, from everyday consumer items to intricate components used in various industries such as automotive, electronics, and medical devices. These tools allow manufacturers to produce complex shapes and designs with precision and efficiency.
Understanding Plastic Molding
Plastic molding is a manufacturing process where raw plastic is heated until it liquefies and is then injected or poured into a mold to form the desired shape. This process not only allows for greater flexibility in design but also enables mass production at relatively low costs. Here are some common types of plastic molding processes:
- Injection Molding: This is the most widely used plastic molding process, where molten plastic is injected into a mold under high pressure.
- Blow Molding: Used for making hollow plastic parts, blow molding involves inflating a heated plastic tube like a balloon inside a mold.
- Rotational Molding: This process involves rotating a mold while plastic granules are heated and then allowed to cool, creating hollow, seamless products.
- Compression Molding: In this method, plastic is placed in a heated mold and then compressed to form the final shape.
Key Components of Plastic Molding Tools
A successful plastic molding operation relies on several core components of plastic molding tools. Understanding these components can help businesses optimize their manufacturing processes.
1. Molds
The mold is the most critical component in the plastic molding process. Molds are typically made from steel or aluminum and are designed to form the shape of the final product. The quality of the mold directly affects the finish and precision of the final product. Factors to consider when designing molds include:
- Cooling Channels: Properly designed cooling channels help in controlling the temperature of the mold, which affects the cycle time and quality of the molded part.
- Tolerance Levels: Molds must be designed with precise tolerances to ensure that the final parts fit together as intended, minimizing waste and rework.
- Durability: Choosing the right materials and processes for mold construction can greatly influence the life span and reliability of the mold.
2. Injection Systems
The injection system is responsible for feeding the molten plastic into the mold. It typically consists of a hopper, screw, and nozzle. Here are key considerations:
- Screw Design: The design of the screw can affect the mixing and temperature of the plastic, thereby influencing the quality of the final product.
- Nozzle Type: The choice between different nozzle types can affect the flow of plastic, thus impacting production speed and quality.
3. Temperature Control Systems
Effective temperature control is essential for ensuring that plastic molds operate within optimal temperature ranges. This can involve:
- Heating Elements: These are used to maintain the mold's temperature during the injection process.
- Cooling Systems: Essential for controlling cycle times and preventing defects in molded parts by ensuring the material solidifies properly.
Benefits of Using High-Quality Plastic Molding Tools
Investing in high-quality plastic molding tools offers numerous advantages that lead to increased productivity and profitability:
1. Enhanced Productivity
Quality tools allow for faster production cycles, resulting in more products manufactured over the same period. This is crucial for meeting market demands without compromising on quality.
2. Improved Product Quality
Precision in manufacturing leads to higher quality products. High-quality molds and tools reduce the likelihood of defects, ensuring that products meet the necessary standards and specifications.
3. Cost-Effectiveness
While the initial investment in quality tools may be higher, the long-term savings on maintenance, repairs, and lower defect rates can significantly offset these costs. This results in a better return on investment.
4. Flexibility in Design
Advanced plastic molding technology allows manufacturers to explore intricate designs and shapes that would otherwise be impossible, providing a competitive edge in product offerings.
5. Environmental Compliance
Modern plastic molding tools can be designed to optimize material usage and reduce waste, helping businesses comply with environmental regulations and reduce their carbon footprint.
Choosing the Right Plastic Molding Tools for Your Business
Selecting the appropriate plastic molding tools involves careful consideration of several factors. Here are some tips to guide your decision-making process:
1. Understand Your Product Requirements
Define the specifications of the products you intend to create. Factors such as size, complexity, and material requirements should influence the type of molding tool you choose.
2. Evaluate the Type of Molding Process
Different products and materials may require different molding processes. It’s essential to assess which method (injection, blow, rotational, or compression) aligns best with your production needs.
3. Consider Future Production Needs
Plan for scalability. Choosing tools that can adapt to future production increases or new product lines will save time and resources in the long run.
4. Assess Tooling Suppliers
Partnering with a reputable supplier, such as deepmould.net, can ensure that you have high-quality tools that meet your production standards. It’s advisable to research and seek testimonials from other customers.
The Future of Plastic Molding Tools: Trends to Watch
As technology advances, so does the realm of plastic molding. Here are some key trends shaping the future of plastic molding tools:
1. Automation and Industry 4.0
Automation is transforming manufacturing processes by enhancing efficiency and minimizing human error. Smart molding tools integrated with IoT technology can provide real-time data for process optimization.
2. Sustainable Practices
Manufacturers are increasingly seeking sustainable and eco-friendly materials for their products. The development of biodegradable plastics and recycling technologies are changing the criteria for choosing molding tools.
3. Advanced Materials
The rise of advanced composite materials necessitates the evolution of molding technologies to accommodate different thermal and mechanical properties, impacting tool design and production methods.
4. 3D Printing Integration
3D printing technology is gaining traction in creating molds and production parts. Integrating traditional molding processes with 3D printing can optimize production flexibility and reduce costs.
Conclusion
In conclusion, plastic molding tools are indispensable in the manufacturing landscape, particularly for businesses in metal fabrication and plastics processing. By understanding their applications, benefits, and the latest trends, manufacturers can harness these tools to enhance productivity, improve product quality, and ultimately drive profitability. With the right approach and tools, your business can not only thrive but also lead in innovation and efficiency in a competitive market.
For more information on high-quality plastic molding tools and solutions, visit deepmould.net.